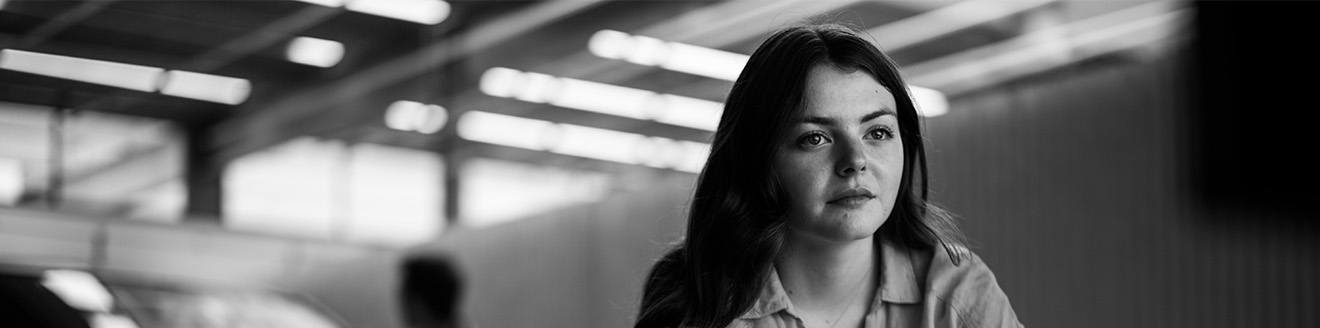
This review was submitted over 4 years ago, so some of the information it contains may no longer be relevant.
Rating
-
The Role
-
The Company
-
The Culture
- 1. To what extent did you enjoy your work placement or internship?
- 2. To what extent did you feel valued by your colleagues?
- 3. To what extent were you given support and guidance by management/your supervisor(s)?
- 4. How busy were you on a daily basis?
- 5. How much responsibility were you given during your placement?
- 6. To what extent did/will the skills you developed, and training you received, assist you in your degree studies and beyond?
- 7. What was the general atmosphere in your office?
- 8. How well organised was the overall work placement or internship set up?
- 9. In terms of personal training and development, to what extent did the company or firm invest in you?
- 10. What were the perks on your work placement?
- 11. How appealing are future employment prospects within the organisation?
- 12. Was there a good social scene amongst any fellow placement students/colleagues?
- 13. What was the cost of living and socialising in the area you worked in?
- 14. What was the Nightlife like in the area you worked?
- 15. Were there many opportunities to get involved in activities outside of work?
The Role
My time at Jaguar Land Rover was very enjoyable, I worked in manufacturing which was a hectic few months but provided me with the opportunity to contribute to the teams work everyday which was usually fresh issues meaning the job was never boring. There was always a lot to learn and take in, I feel that I've been fully exposed to all parts of vehicle production thanks to tours and being given jobs that spanned the whole plant.
Everyone at the company is very welcoming and views you as a peer and not as a student. I integrated very quickly and would say that if you put the effort in you will be rewarded in terms of making relationships within the company. The ethos of the company is to avoid email if possible and have constructive conversations to problem solve, this was nice to know that anyone is willing to chat with you to help.
You are usually placed with a manager in an LL6 position but from my experience and talking to other interns there isn't much contact as they are usually busy in their roles. Instead you are usually given a mentor (D grade engineer) who was very helpful and guided me through my first few weeks here. However because your LL6 manager signs off your progress at the end there feels like a slight disconnect as they may not know what you have worked on and contributed to.
Manufacturing itself is a busy industry with lots of daily reviews and meetings to track key metrics which I attended. I was also given responsibilities of providing reports for suppliers and conducting investigations on out-of-spec parts which kept me busy. On top of this I had a project that spanned my placement about justifying an inspection process and seeing if improvements could be made.
As the placement went on and I gained the trust of my colleagues I was given more responsibility, including dealing with suppliers at meetings and providing metric reports for those meetings. Whilst daunting, these tasks taught me to prepare for unforeseen troubles and helped me problem solve under pressure when deadlines have to be met.
In terms of my degree I feel that I have a full grasp of the whole manufacturing process and how a lot of it is not just designing processes to be done but improving on those processes with problem solving to increase the quality of the product. I hope to go into product development so I feel that manufacturing experience will give me a different approach than others in terms of design and process.
The Company
Friendly and welcoming, you are encouraged not to email but to talk to colleagues, it's easy to chat to people of all ages and learn about their roles. Everyone has expressed an interest in what my role is and what I will do after my placement finishes. Every day there was a morning meeting to discuss everyone's concerns and have a friendly chat also.
There is an induction with every undergraduate then a site induction, helping you to network and make friends from the start. You have the opportunity to use Catalyst which is an online learning tool with many courses, There is also a full review process which your manager signs off, and if you have performed well then you will almost be guaranteed a place on the graduate scheme next year which is very reassuring.
There was a full 2 week course available about LEAN manufacturing which I would have liked to attend but wasn't able to because of the timing and length of my placement. But having catalyst to help develop your skills and knowledge was useful and I was given time to use this resource to learn and develop.
Flexi Time
Subsidised Canteen
Company Parties/Events
Very appealing, great graduate salary with a set scheme. There also looks like there is a definite path for career progression if you are willing to work hard and contribute to the company. Everyone here seems happy with their roles and there is the opportunity to move around the business if you feel a role is becoming to stale for you.
The Culture
At the Halewood manufacturing site there was only 9 undergraduates there but we organised our own nights out and weekend activities like go karting. There wasn't much set up for us because the majority of the undergraduates are at the Whitley or Gaydon sites.
I lived at home near Liverpool, which is quite a cheap place to go to for socialising. The housing near to the manufacturing site is not too expensive from what I have heard and the public transport links are pretty good.
Liverpool nightlife is great but I'm biased because I live near Liverpool so go there very often. Lots of clubs and places to go and is busy on Saturdays and Thursdays for students.
There is an employee learning scheme which grants you £200 a year to spend on outside activities. However I spent it on driving lessons which I had not had before, this scheme is excellent and so easy to use and was a massive perk to the job.
Details
Internship (1 Month+)
Automotive Engineering, Manufacturing
North West
August 2016