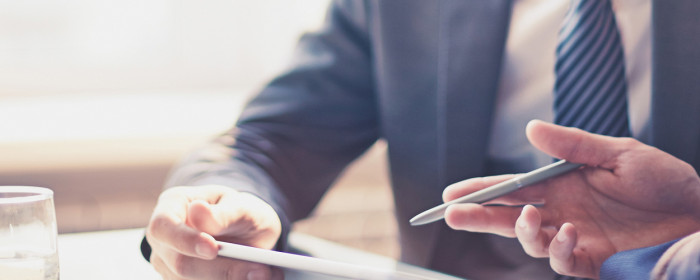
Rating
-
Skills
-
Responsibilities
-
Support & Guidance
-
Culture
-
Your Impressions
- 1. Please give an overview of your role and what this involves on a day-to-day basis.
- 2. Have you learnt any new skills, or developed your existing skills?
- How would you rate the training provided during your experience?
- How would you rate your development of industry-specific skills during the experience?
- How would you rate your development of personal / soft skills during the experience?
- Please rate how these skills have helped you in your career development
- 3. Were you given much responsibility during your placement / internship?
- Please rate how meaningful the work you were doing was
- 4. How much support and guidance did you receive during your placement / internship?
- How would you rate the support and guidance from your line manager?
- How would you rate the support and guidance from the wider team?
- 5. What was the company culture and general atmosphere like?
- How would you rate the inclusiveness of the culture?
- How would you rate the social opportunities?
- How would you rate the diversity initiatives?
- How would you rate the charity, sustainability and corporate social responsibility (CSR) initiatives?
- 6. To what extent did you enjoy your placement / internship?
- Please rate your level of enjoyment on your placement / internship
- Please rate how your experience met your expectations
- Please rate the future employment prospects at Forvia
- 7. Would you recommend Forvia to a friend?
- 8. What advice would you give to others applying to Forvia
Overview
In this role you are responsible for 5S audit data collection and leading 5S workshops. You will also be involved in other improvement workshops such as DLE max workshops and SMED workshops. Taking cycle times and creating cycle time diagrams is also a large part of the role. Then analysing these and rebalancing workload of the operators. You will lead a weekly improvement idea meeting with the other students and decide which improvement ideas to implement. The implementation of various improvement ideas around the plant is a large part of the role. Also you will support the deployment of FES X.0 with a specific focus on Production Systems.
Skills
The main skills I have developed are leadership, autonomy and my presenting skills. I developed leadership skills from leading a weekly improvement idea meeting and delegating tasks to various people in the meeting. Also from leading a 5S workshop where I had to delegate and follow up on assigned tasks too. I developed autonomy throughout the year as no one holds your hand. You are let know what you need to do and then left to do it. It has been up to me to complete work on time which has also improved my time management skills. In this role at the end of each month I have prepared a presentation containing all the implemented improvement ideas from the last month which I have presented to management. This has improved my presenting skills massively,
Responsibilities
I have been given probably the correct amount of responsibility for a student. I have been responsible for collecting and uploading data, leading a weekly meeting, presenting a monthly powerpoint and taking cycle times. I have been given enough responsibility to make me feel needed by the business but not too much that it has become overly stressful. The main responsibly I have been given is managing my projects by myself, and being trusted to ensure they are completed on time.
Support & Guidance
I have been given enough support to feel comfortable and sort of know what I need to do. But have been left to figure alot of tasks out on my own. This has been good in a sense as I have had to figure alot of stuff out on my own which has helped me learn more and also made it more interesting. There has always been support there however if I've had any questions.
Culture
The company has an improvement ideas culture/mindset. There is an improvement ideas tracker which you are responsible for in the FES&P role. Everyone can submit their ideas and see the improvements site wide. The operators like to complain alot but I guess that is common across most manufacturing plants. Everyone is very welcoming when you first start and easy to talk to. Also being at Fradley FCM it is a relatively small plant so you get to know everyone quickly.
Your Impressions
I have really enjoyed my placement year. The best thing has to be the people I have worked with. Everyone is friendly and welcoming and there are some great characters in the office. I have enjoyed being in FES&P as the role has allowed me to use my hands on skills for implementing improvement ideas aswell as analytical skills for improving processes. Overall it's a perfect role for any engineering minded student that also likes hands on work.
Yes
The application process is relatively simple. You go to an assessment center where you amongst other teamwork tasks you complete a numerical and personality test. Then it's straight to an interview with your line manger and HR if you get through that so it's relatively quick. I'd say be confident throughout the process and really project what you can offer the company. Also, make sure you do your research on what the company does before you apply!
Details
Placement (10 Months+)
Mechanical Engineering
West Midlands
August 2021