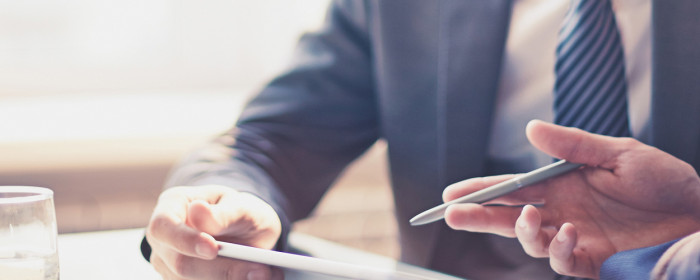
Rating
-
Skills
-
Responsibilities
-
Support & Guidance
-
Culture
-
Your Impressions
- 1. Please give an overview of your role and what this involves on a day-to-day basis.
- 2. Have you learnt any new skills, or developed your existing skills?
- How would you rate the training provided during your experience?
- How would you rate your development of industry-specific skills during the experience?
- How would you rate your development of personal / soft skills during the experience?
- Please rate how these skills have helped you in your career development
- 3. Were you given much responsibility during your placement / internship?
- Please rate how meaningful the work you were doing was
- 4. How much support and guidance did you receive during your placement / internship?
- How would you rate the support and guidance from your line manager?
- How would you rate the support and guidance from the wider team?
- 5. What was the company culture and general atmosphere like?
- How would you rate the inclusiveness of the culture?
- How would you rate the social opportunities?
- How would you rate the diversity initiatives?
- How would you rate the charity, sustainability and corporate social responsibility (CSR) initiatives?
- 6. To what extent did you enjoy your placement / internship?
- Please rate your level of enjoyment on your placement / internship
- Please rate how your experience met your expectations
- Please rate the future employment prospects at Forvia
- 7. Would you recommend Forvia to a friend?
- 8. What advice would you give to others applying to Forvia
Overview
As a quality placement student I was working with the Supplier Quality Engineer leading supplier improvements tracked using 8D methodology and ensured effective containment of any NOK stock on our production line via a 3rd party sorting company. This involved having weekly meeting with suppliers from over 4 different continents. I was also in charge of the supplier returns process for any defective parts and/or samples which needed to be returned. This involved using SAP to create the correct paperwork and stock transfers for the return. Further to this, I was involved in scrap reduction. I lead two meetings the weekly meeting and the morning meeting known in the company as ‘The Morning Market.’ This is where we reviewed any previous actions and analysed the previous days scrap to align trends and based on these trends new actions were set for the day; aligning to the companies beliefs on QRCI and Zero defect mentality. Moreover, I was involved in rework reduction where I collected, analysed and presented rework data weekly to report on problem areas. I also was involved in updating production documentation as a result of customer concerns. This involved updating PFMEA, Work Instructions and Control Plans.
Skills
Before working for Faurecia, I had not written reports or conducted presentations on a large scale. I found it particularly difficult to document the ‘important’ information into the presentation and to keep it concise. Further to this, I was not very confident in the information I was displaying which meant when I presented I came across unsure and the clarity of the presentations were compromised. I decided to practice in my personal time and eventually found the presentations I was creating were able to display important information and started applying the 80:20 rule. As I progressed in my placement, I became much more confident in what I was displaying and this meant I was able to contribute more engineering detail and analysis to the meetings. Improved on my technical knowledge of welding, through several training sessions.
Responsibilities
During my time at Faurecia I have helped develop numerous solutions to supplier concerns, customer concerns, scrap reduction and rework reduction. I was involved and started leading weekly meeting with high risk suppliers across the world to improve overall performance and to develop robust improvement plans. I was actively tracking their improvements and helping them improve their processes, methods and accuracy. In respect to customer concerns I have helped develop solutions that are both preventative (Poka-Yokes) and detective (end of line method of check). An example of a detective solution I have helped implement is a ‘plug gauge’ this is used to test the inner diameter too see if there is any over penetration of weld, potentially causing issues for the customer. Further to this, I presented weekly meetings regarding scrap reduction. In these meetings I presented our current situation in respect of scrap. This helped identify potential high risk supplied components, tooling issues and/or weld trajectory issues. I then collated actions and targets made in these meetings into a PDCA, where I tracked progress on open topics and held people accountable for their deadlines. In regards to rework reduction, again I presented a weekly meeting showing our current situation. I took on actions regarding supplied components such as CPK and PPK measurements.
Support & Guidance
I found that at the very start of my placement there was no handover due to coronavirus and this meant the amount of support and guidance that I received in my first month was very limited. I had to seek out information for myself and try to understand the work I was being asked to complete. However, I received some guidance and direction when it came to supplier notifications for the SQA at the time.
Culture
The culture of the business was very open and accepting and with no office politics to spoil the atmosphere within the workplace. This in turn meant that the office had a real team spirit about it. With Faurecia being so open it meant we could follow the Faurecia values of integrity and honesty, Respect and Accountability. The fact that the business was so accommodating meant that everyone was give the opportunity to be autonomous and show entrepreneurship.
Your Impressions
Throughout my placement with Faurecia, I enjoyed many aspects of the role such as: collaboration, work-life balance, autonomy, variety and challenge. Everyone in Faurecia shares the same values and vision. The collaborative environment in FCM Fradley allowed me to learn the importance of having a multi-disciplinary team. One of the main things I enjoyed about my time at Faurecia was the work-life balance that I was able to achieve. Throughout my time at university and school I would always be working on weekends and late into the evening studying. However, throughout the placement I have been able to have more freedom to explore the local area (despite covid restrictions). Before coming to Faurecia, I was worried that I would not be able be an independent employee as I had not worked before but becoming independent and autonomous in my approach to work has gave me a lot of job satisfaction as this was one of my main objectives. The variety of projects I have been able to get involved with has been brilliant and the amount of exposure I have had within the business has been amazing. The numerous projects that I was involved in did come with its challenges. However, this is one of the things I enjoyed about them as it makes the work just that more exciting and interesting.
No
The advice i would give to prospective new placement student would be: - Ensure you know Faurecia Values - About the business (i.e current event or intiatives) - Experience in automotive is not necessary - Make sure you ask questions at your interview - Make sure you CV and covering letter show how you will add value to the business. - If you need help, ask for it. I believe the above points are what are important to applying to Faurecia. -
Details
Placement (10 Months+)
Mechanical Engineering
West Midlands
August 2021