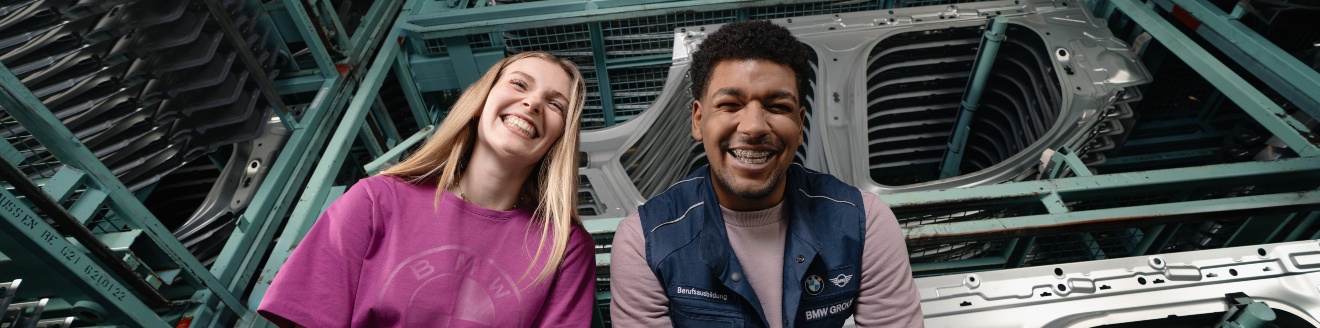
Rating
-
Skills
-
Responsibilities
-
Support & Guidance
-
Culture
-
Your Impressions
- 1. Please give an overview of your role and what this involves on a day-to-day basis.
- 2. Have you learnt any new skills, or developed your existing skills?
- How would you rate the training provided during your experience?
- How would you rate your development of industry-specific skills during the experience?
- How would you rate your development of personal / soft skills during the experience?
- Please rate how these skills have helped you in your career development
- 3. Were you given much responsibility during your placement / internship?
- Please rate how meaningful the work you were doing was
- 4. How much support and guidance did you receive during your placement / internship?
- How would you rate the support and guidance from your line manager?
- How would you rate the support and guidance from the wider team?
- 5. What was the company culture and general atmosphere like?
- How would you rate the inclusiveness of the culture?
- How would you rate the social opportunities?
- How would you rate the diversity initiatives?
- How would you rate the charity, sustainability and corporate social responsibility (CSR) initiatives?
- 6. To what extent did you enjoy your placement / internship?
- Please rate your level of enjoyment on your placement / internship
- Please rate how your experience met your expectations
- Please rate the future employment prospects at BMW Group UK
- 7. Would you recommend BMW Group UK to a friend?
- 8. What advice would you give to others applying to BMW Group UK
Overview
The role involves the use of metallurgical analytical methods, combined with metallurgical knowledge to provide consult to process partners as needed during production and development. This would include visual and microscopic analysis, alongside more hands-on aspects through sample preparation, and subsequent sample quantification. Throughout the year, a project is also assigned to span the length of the placement, with a presentation/report at the end, as well as opportunities to present and gain feedback.
Skills
Key skills: - Manual dexterity due to the extensive amount of hands-on work - Metallurgical knowledge due to the large amount of knowledge available from superiors and existing report database - Networking and communication due to meetings with process partners throughout the BMW group - Ability to learn bespoke software on the fly, as the hardware for testing included software to operate and process results
Responsibilities
From the start, the training was thorough, with the team taking every opportunity to show you how to use the range of equipment. This was prevalent through the 1-month handoff period from the previous intern, which not only included training, but also some supervised handling of the equipment. Responsibility was also provided through the individual project, which was internal, though previous intern projects have been external, allowing for more responsibility to network and communicate.
Support & Guidance
Guidance was readily available as the team were always on hand, even if working from home. Additionally, several members of the chemistry team (Shared lab), were also equipped with knowledge and experience of the metallurgical side, so could provide consult at times where primary contacts were unavailable.
Culture
The company culture was fantastic, with a lot of opportunities to communicate and network with people from other departments, due to their reliance on my reports to quantify their next steps given a problem.. However, there would oftentimes be hostility from other departments when the results were not what they wanted (i.e. out of spec). This was combatted through the support of superiors and my line manager.
Your Impressions
I enjoyed it thoroughly - when there was work to do. The big issue with the role is that it is on an ad-hoc basis, and I came at a time when they were planning the transition to another engine manufacture phase. This meant that the majority of issues that could occur, had already been addressed, and any further issues would be due to manual handling rather than material faults.
Yes
When applying, they do not care as much for your university identity, or your degree past the point that you would expect. They want your education to get your foot in the door and get you past screening, but the managers clearly care more about your personality and ability to work with others, and efficiency when working alone.
Details
Placement (10 Months+)
Chemical Engineering, Engineering, Mechanical Engineering
West Midlands
November 2021