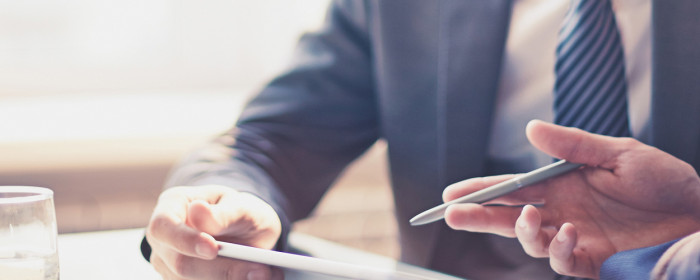
Rating
-
Skills
-
Responsibilities
-
Support & Guidance
-
Culture
-
Your Impressions
- 1. Please give an overview of your role and what this involves on a day-to-day basis.
- 2. Have you learnt any new skills, or developed your existing skills?
- How would you rate the training provided during your experience?
- How would you rate your development of industry-specific skills during the experience?
- How would you rate your development of personal / soft skills during the experience?
- Please rate how these skills have helped you in your career development
- 3. Were you given much responsibility during your placement / internship?
- Please rate how meaningful the work you were doing was
- 4. How much support and guidance did you receive during your placement / internship?
- How would you rate the support and guidance from your line manager?
- How would you rate the support and guidance from the wider team?
- 5. What was the company culture and general atmosphere like?
- How would you rate the inclusiveness of the culture?
- How would you rate the social opportunities?
- How would you rate the diversity initiatives?
- How would you rate the charity, sustainability and corporate social responsibility (CSR) initiatives?
- 6. To what extent did you enjoy your placement / internship?
- Please rate your level of enjoyment on your placement / internship
- Please rate how your experience met your expectations
- Please rate the future employment prospects at Forvia
- 7. Would you recommend Forvia to a friend?
- 8. What advice would you give to others applying to Forvia
Overview
My role involved two main areas: scrap & rework, and supplier quality. On a daily, weekly and monthly basis I monitor the scrap and rework data to identify trends and top issues for the engineering team as a part of lean manufacturing. My placement has also been heavily based in supplier quality, which involved monitoring the quality of parts received and comparing the true condition to the drawing. This involved communication with international suppliers to ensure any issue were addressed and the manufacturing line was not affected. I have also been working to quantify supplier performance and rank our worst suppliers so we can work with them to drive improvements.
Skills
I have definitely improved my confidence and communication skills, both written and verbal. I am also now much more comfortable with analysing engineering drawings - something we touched upon in my degree but I now find them a lot easier to navigate to find the relevant information. Attention to detail has also been vital as the tolerances can be as small as a fifth of a mm, so any small change in the parts can impact the manufacturing line.
Responsibilities
Yes. I wanted a placement where I was able to make an impact and I can definitely see this here. I created process for supplier ranking and random inspection which are now used and can be taken forward and developed by the next student. I was also responsible for the management of all quarantined stock, and for supplier returns of NOK parts. This stock has a target of thousands of pounds. Additionally, I manage the scrap and rework data which is an important plant KPI (Key performance indicator).
Support & Guidance
We had a two week hand-over period. Training is also provided by MOOCs and regular programmed sessions. However, there were times at the beginning where I felt I needed more support and training. This role has a lot of responsibility, and some of the processes (such as supplier returns) is quite difficult due to customs complications and multiple stakeholders. Perhaps I needed to be more vocal in asking for support, but I would have appreciated a mentor or guide during my training - a dedicated person other than my manager I could ask questions to.
Culture
Forvia had a couple of celebration events which were quite enjoyable. This included a yearly "Forvia day". We (the students) also worked together on the Charity challenge and organised events to raise money for Young lives against Cancer. All the people who work here have become friends and I enjoy working with them. However, the automotive industry has been struggling a little since covid and due to the semiconductor shortage. This has lead to some negativity in the workplace. With that being said, this may just be unlucky timing, as the industry is expected to start to pick up again this year.
Your Impressions
The work was interesting and I am glad to have made a meaningful contribution. The responsibility level did at one point cause me to feel overloaded. However, I was able to talk to my manager and calm some of my worries and get through this low point. I enjoy the team I work in, and the people I have worked with. Additionally, being a woman in a manufacturing environment (90% male employees) was something that worried me. However, I was never treated any differently from my male counterparts and it is not something I notice any more. I am not currently planning to come back to Faurecia as I am not sure automotive is for me. I wanted this placement to learn more about the manufacturing environment, which I definitely have, but now I would like to find some opportunities more relevant to my field.
Yes
If you are concerned about gender diversity, it is an issue, but I have not found it to affect me. For the interview and assessment centre, all I can advise is slightly generic - be authentic and be clear about why you want this placement. There is a lot to learn once you get on the job, which can be daunting. I imagine this is the same with most jobs but it will take you a while to get into the role and make it your own. This is normal so don't loose hope!
Details
Placement (10 Months+)
Automotive Engineering, Manufacturing
West Midlands
August 2022